Relay Used in Industrial Control
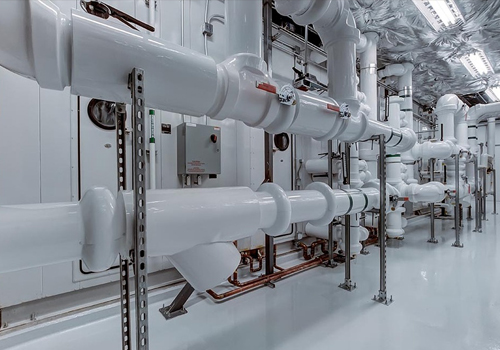
In industrial control, the main control functions are completed by general-purpose AC relays. Relays are usually driven by pushbuttons or limit switches. The contacts of the relay can control the solenoid valve, the larger starter motor, and the indicator light. The voltage is generally 24VDC, 220VAC. The field of digital control has expanded the application of relays. Copy milling and coordinate boring are operated by data programming, and the signals are sent to the machine tool controller, memory unit and other logic elements to control the 2 to 5 axes of the coordinate servo motor. With this automatic control method, it is easy to control drilling machines, hexagonal lathes, ordinary lathes and automatic profiling machines.
One of the primary functions of relays in industrial control is to amplify and isolate signals. When a low-voltage control signal is insufficient to directly control a high-power device, a relay acts as an intermediary, amplifying the signal to trigger the necessary action. Moreover, relays provide electrical isolation, preventing the control circuit from being affected by the high-power load, enhancing the overall safety and reliability of the system.
Furthermore, the longevity and durability of relays make them ideal for industrial environments characterized by harsh conditions. Relays can withstand temperature extremes, high humidity, and mechanical vibrations, ensuring a stable and continuous operation in challenging settings.
Digital control systems require relays with low-level signal adaptability, moderate sensitivity, fast action, and high switching reliability. The environmental conditions of industrial machinery installation must be considered. Running industrial machinery and nearby equipment always transmit some shock and vibration to the control cabinet; there is also the possibility of splashing cutting coolant. Usually equipment manufacturers take certain protection measures for control components, but these unfavorable environmental conditions should still be considered when selecting and designing relays. The safety requirements are strict, and there are higher requirements for electrical insulation, voltage resistance, and flame retardancy.
In conclusion, the role of electrical relays in industrial control cannot be overstated. These versatile devices form the backbone of automation, ensuring the seamless and safe operation of complex industrial processes. As industries embrace technological advancements, the humble relay stands resilient, proving to be an indispensable component in the ever-evolving landscape of industrial control systems.
One of the primary functions of relays in industrial control is to amplify and isolate signals. When a low-voltage control signal is insufficient to directly control a high-power device, a relay acts as an intermediary, amplifying the signal to trigger the necessary action. Moreover, relays provide electrical isolation, preventing the control circuit from being affected by the high-power load, enhancing the overall safety and reliability of the system.
Furthermore, the longevity and durability of relays make them ideal for industrial environments characterized by harsh conditions. Relays can withstand temperature extremes, high humidity, and mechanical vibrations, ensuring a stable and continuous operation in challenging settings.
Digital control systems require relays with low-level signal adaptability, moderate sensitivity, fast action, and high switching reliability. The environmental conditions of industrial machinery installation must be considered. Running industrial machinery and nearby equipment always transmit some shock and vibration to the control cabinet; there is also the possibility of splashing cutting coolant. Usually equipment manufacturers take certain protection measures for control components, but these unfavorable environmental conditions should still be considered when selecting and designing relays. The safety requirements are strict, and there are higher requirements for electrical insulation, voltage resistance, and flame retardancy.
In conclusion, the role of electrical relays in industrial control cannot be overstated. These versatile devices form the backbone of automation, ensuring the seamless and safe operation of complex industrial processes. As industries embrace technological advancements, the humble relay stands resilient, proving to be an indispensable component in the ever-evolving landscape of industrial control systems.